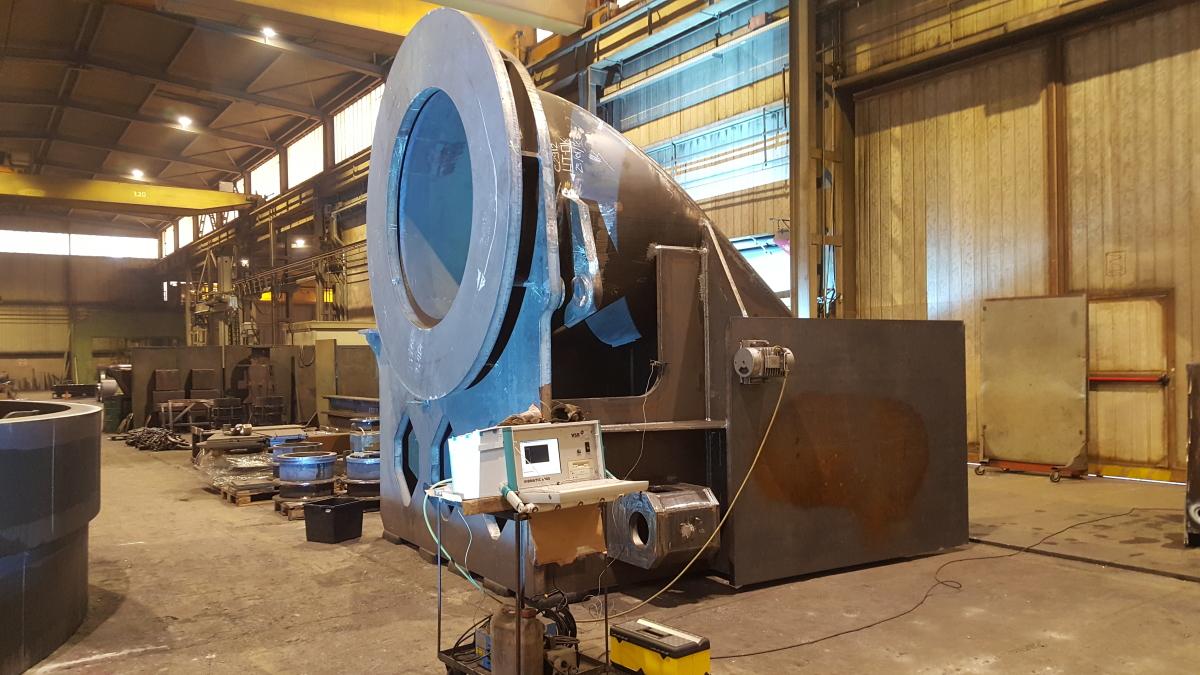
What is Vibration Stress Relief?
The term Vibration-Stress-Relief (VSR) identifies a metal-physical method of dimensional stabilization of a metal component or structure by means of forced vibrations.
In use since the 1960s in the USA, the stress relieving method consists in making a piece vibrate, for a certain period of time and at certain resonant frequencies, thanks to a vibrator engine with variable eccentric masses.
What is Vibration Stress Relief for?
Reduction of residual tensions that occur in each manufactured article that it undergoes
- mechanical processing,
- welds,
- chemical or metallurgical processes.
The risks associated with the presence of residual stresses:
- Distortions of the component following machining operation
- Delayed distorsions
- Fatigue breakages anticipated over time
1. What are residual stresses and what is meant by the release of these stresses?
Residual stress is the internal pressure that is held by the metal after a mechanical or thermal shock, once the source of that stress has been removed. The source of residual stress in the metal can be mechanical (forced change in the shape of the grains) or thermal (sudden drop in temperature). Residual stresses and, in particular, thermally induced stress, cause three types of problems on the metal component:
- Distortions of the component as a result of machining or grinding,
- increased corrosion
- premature failure due to fatigue.
The distension of residual stresses neutralizes the thermally induced stress thus reducing/eliminating the problems listed above. It is not necessary to modify the mechanical properties of the material or the grain structure to obtain the relaxation of the thermally induced residual stresses.
2. How long does a single stress relieving cycle take by mechanical vibrations?
The cycle time of a single treatment varies from 25 minutes to 1 hour. For the complete stress relieving of a component, several vibration stress relieving cycles may be required depending on the weight, dimensions and geometry of the component itself.
3. Are there any weight and size limitations for the vibration treatment?
There is no weight or size limitation regarding the components that can be vibrated. For very small and light components or for very heavy components it will be necessary to provide certain technical measures to make the treatment possible.
4. Are there any limitations due to the type and nature of the component for the feasibility of the vibration treatment?
The vibro-stress process is not effective on components where mechanically induced residual stresses are dominant (such as in cold rolled products). It is not particularly suitable for laser welded, electron beam or spot welded components.
It is not compatible with applications that require the alteration of the properties of the metal itself.
5. What happens inside the component undergoing the vibrations?
The induced vibrations excite the metal so that it oscillates at an energy level higher than normal. When this happens, the areas with a high concentration of tensions use the additional energy brought by the vibration to redistribute the tensions in the areas with a lower concentration; by carrying out this balancing, the overall stress state in the component is reduced/eliminated.
6. Can the vibration treatment be carried out during the welding phase? Which are the advantages?
Yes, the vibrodistension can be used during the welding phase with the following benefits:
- Prevent 50 ÷ 90% of normal distortions due to welding
- Prevent 50 ÷ 90% of breakages due to welding
- Increase the welding speed
- Reduce component preheating
- Reduce the porosity of the weld
Note: the vibrations in this case are so gentle that they do not disturb the operator during the welding phase.
Why rely on Barra Project?
Over 50 years of experience in the use of this technology and an infinite number of geometries and treated materials are our real added value.